Henlo Coffee
Overview
Henlo Coffee's commercial espresso machines integrate advanced technology to ensure superior coffee quality and smart functionality. The machines not only produce exceptional coffee but also offer automated maintenance and business insights. This combination of features positions Henlo machines as a key player in modernizing the coffee industry.
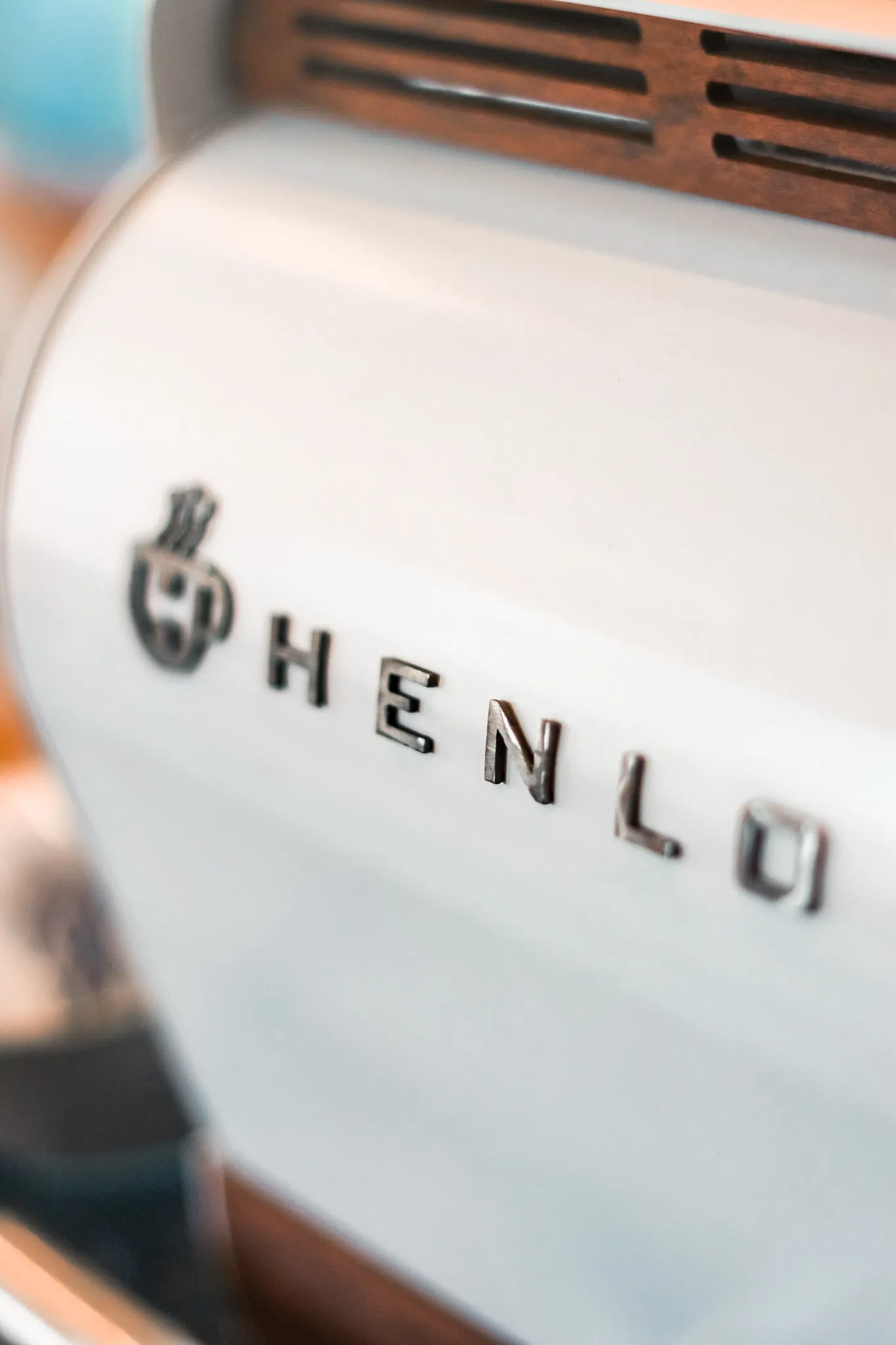
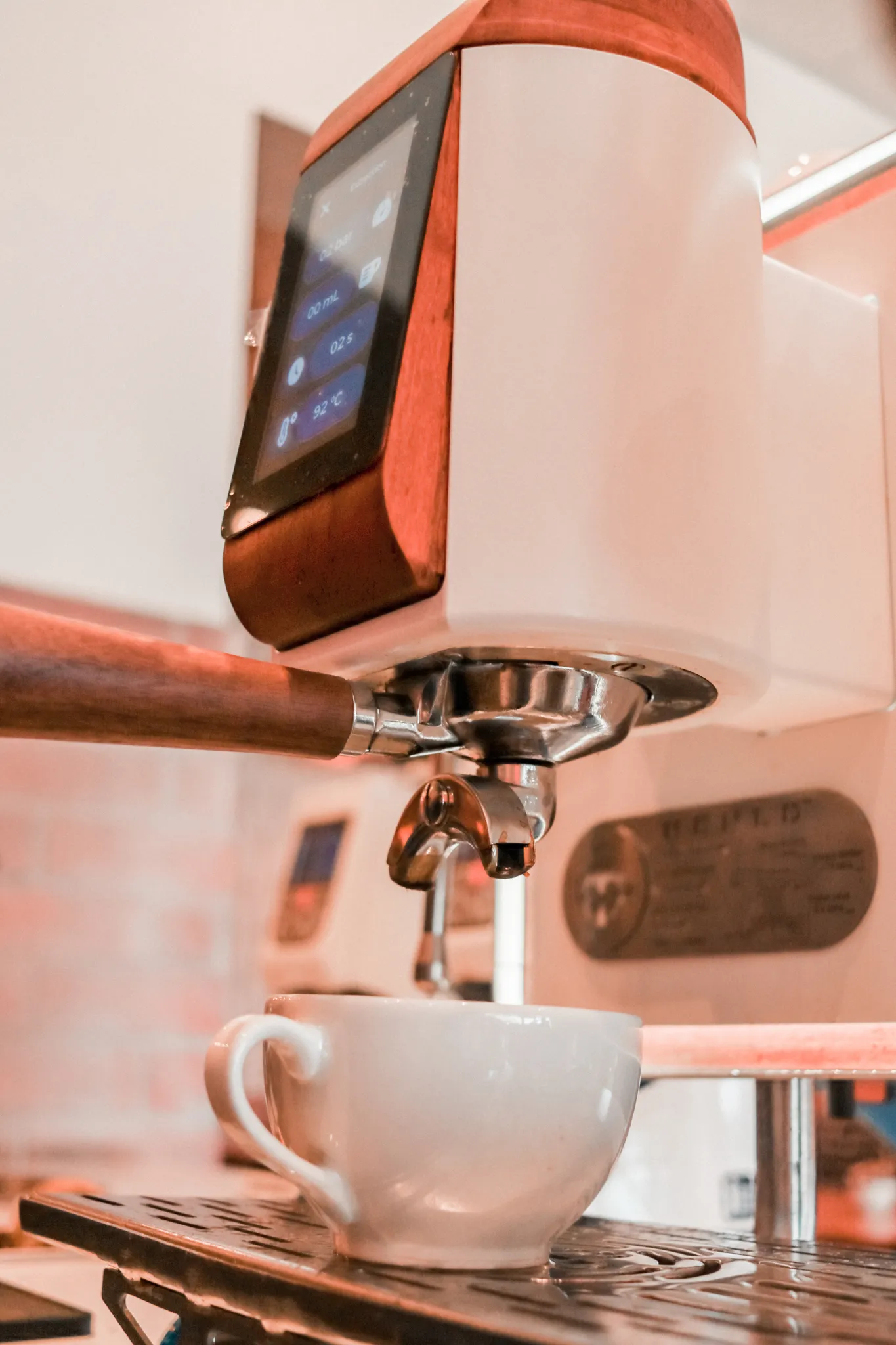
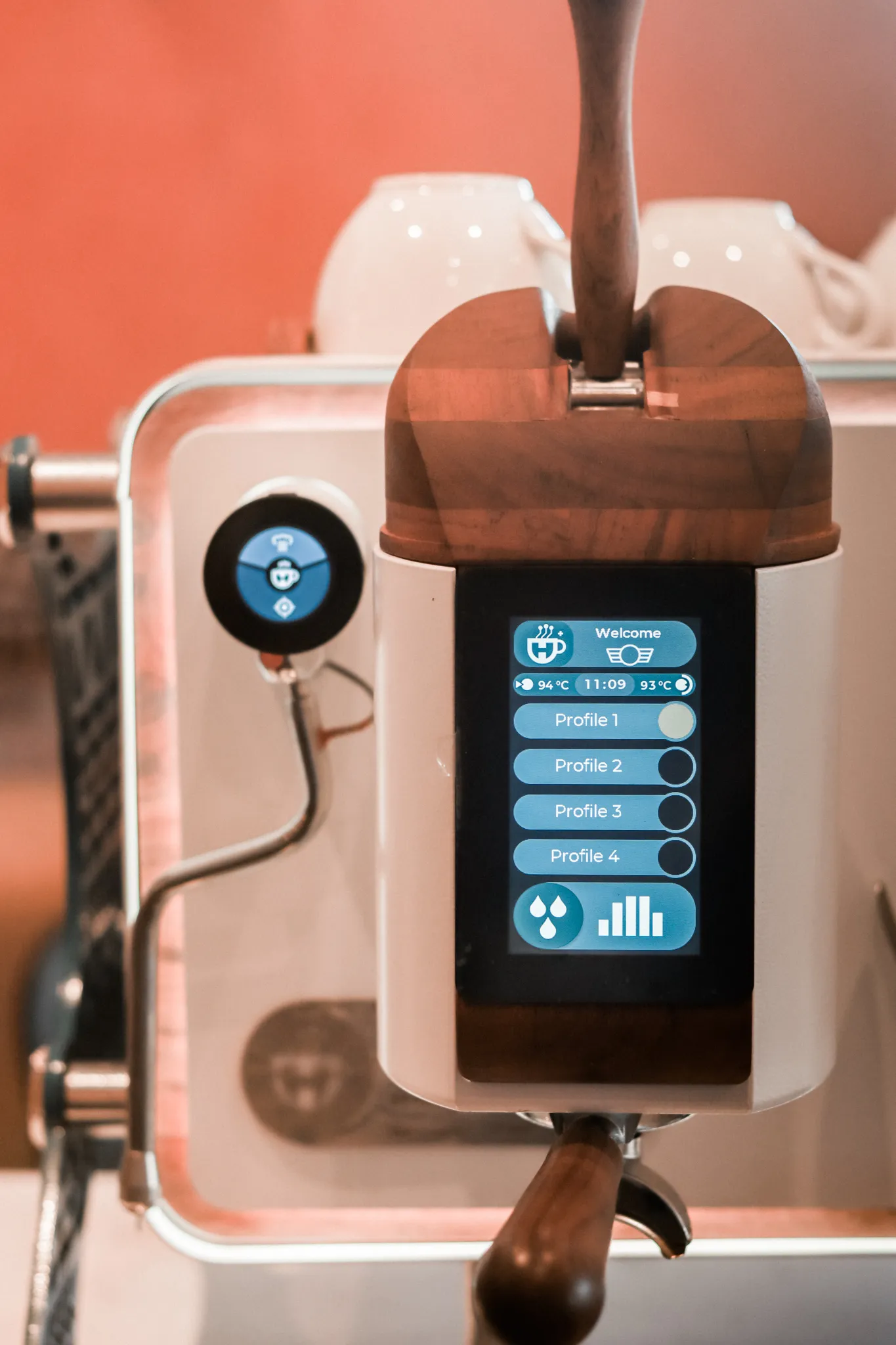
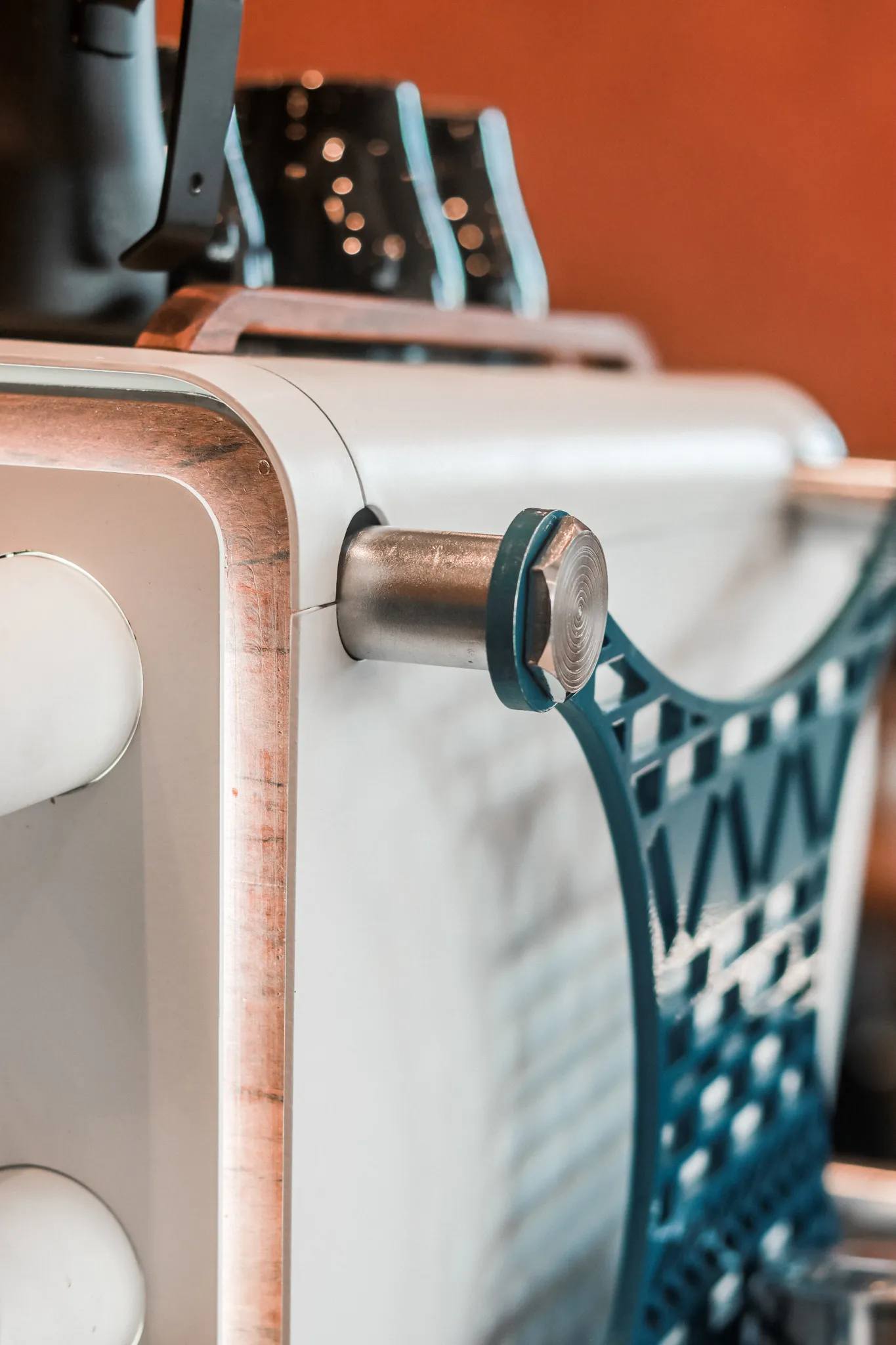
Challenge
Henlo Coffee needed to analyze and repurpose their existing printed circuit boards (PCBs) to develop a prototype of their innovative espresso machine. The initial focus was on understanding and debugging the machine's electronics to identify potential functionalities and address early issues.
Objective
In order to make Henlo succeed, we needed to achieve the following objectives:
- Analyze and repurpose existing PCBs
- Develop a prototype with minimum viable product (MVP) features
- Simplify machine complexity while enhancing functionality
- Transition from high-cost, customizable units to optimized, cost-effective designs
- Incorporate continuous innovation to refine technology and functionality
Solution
Octoco collaborated with Henlo Coffee to analyze their PCBs and develop a prototype. This involved:
- Establishing new building blocks from the ground up
- Iteratively improving the machine through distinct versions
- Engaging baristas for feedback to identify MVP features
- Transitioning from a high-cost, customizable V1 to an optimized V2
- Simplifying the machine's design for easier manufacturing and maintenance
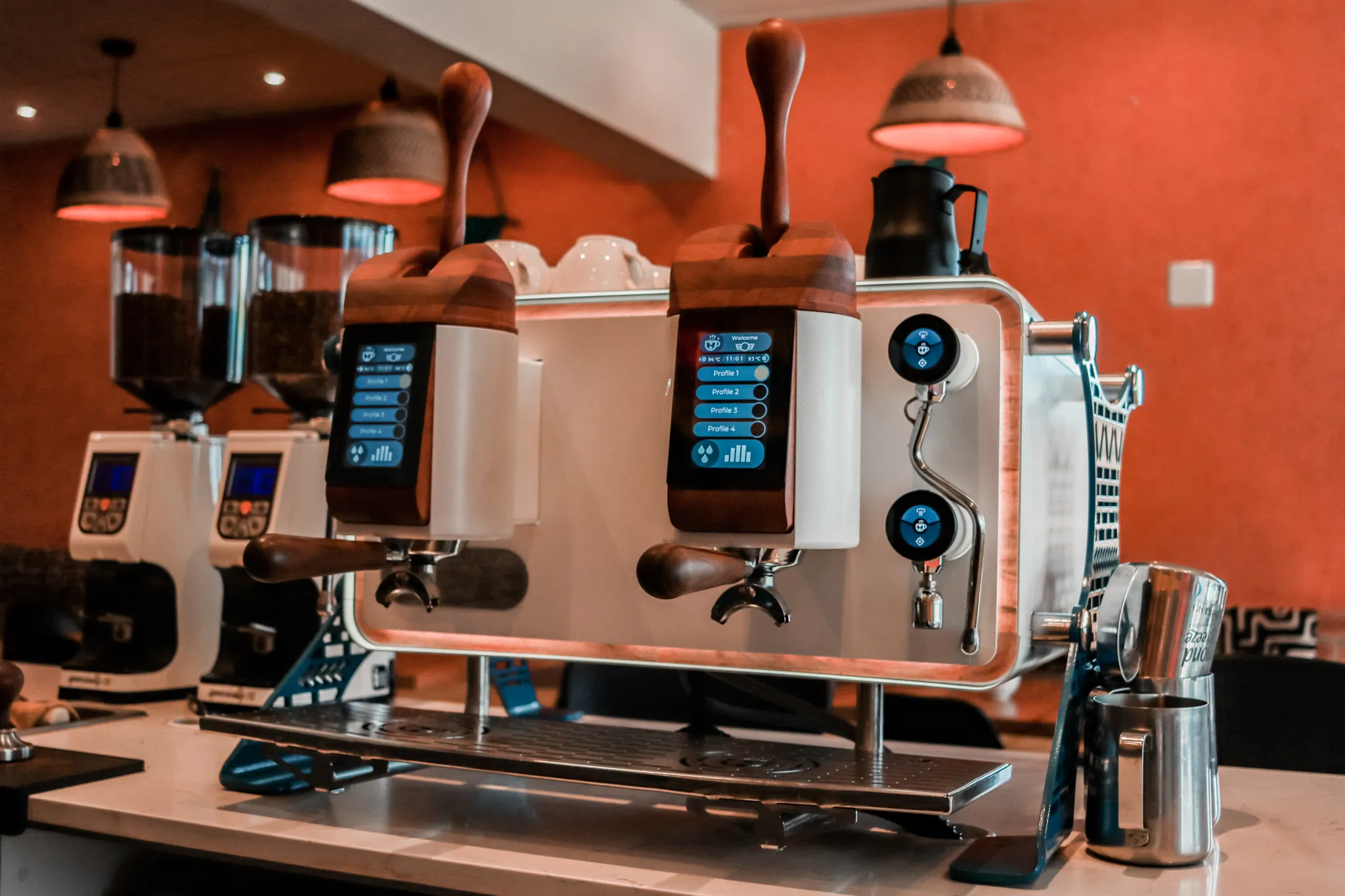
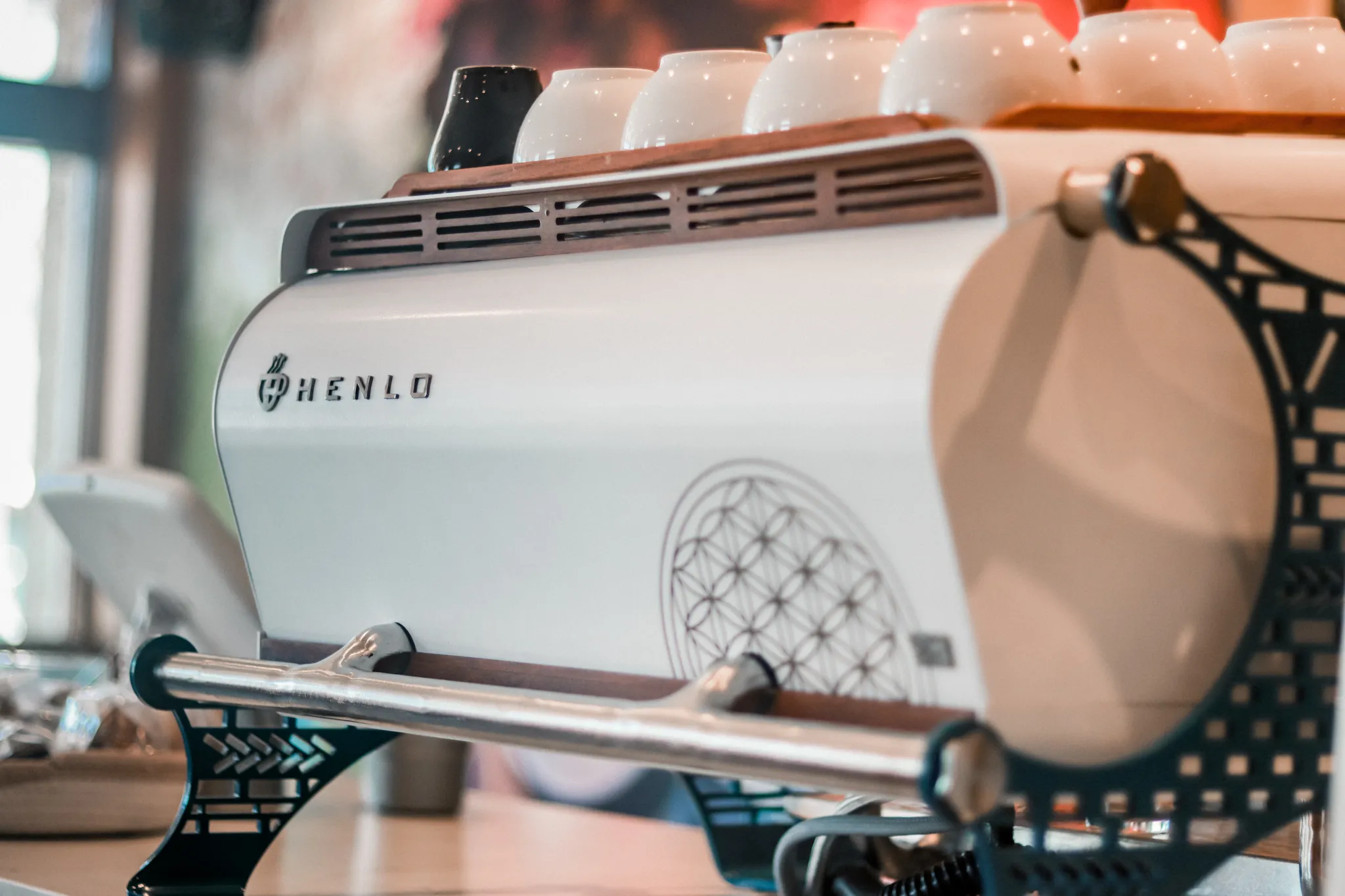
Implementation
The initial focus was on debugging and understanding the machine's electronics. Feedback from baristas was used to identify essential features for the MVP.
The journey progressed through distinct iterations:
Version 1: High costs, extensive customizability (machine colors, wooden legs, laser engravings)
Version 2: Rigorous testing by 100 baristas, producing 6,500 cups in four weeks, optimized supply chain, removal of Bluetooth, shift from mobile platform to web dashboard, stainless steel housing, detachable panels for easier maintenance
Result
The iterative development process led to significant improvements in the espresso machines. V2 showcased optimized design and manufacturing processes, with enhanced serviceability and cost-effectiveness. The forward trajectory involves further PCB alterations and exploring custom solutions with touchscreen interfaces, focusing on continual innovation to meet evolving consumer needs.